Unlocking Innovation with Plastic Rapid Prototyping in Modern Business
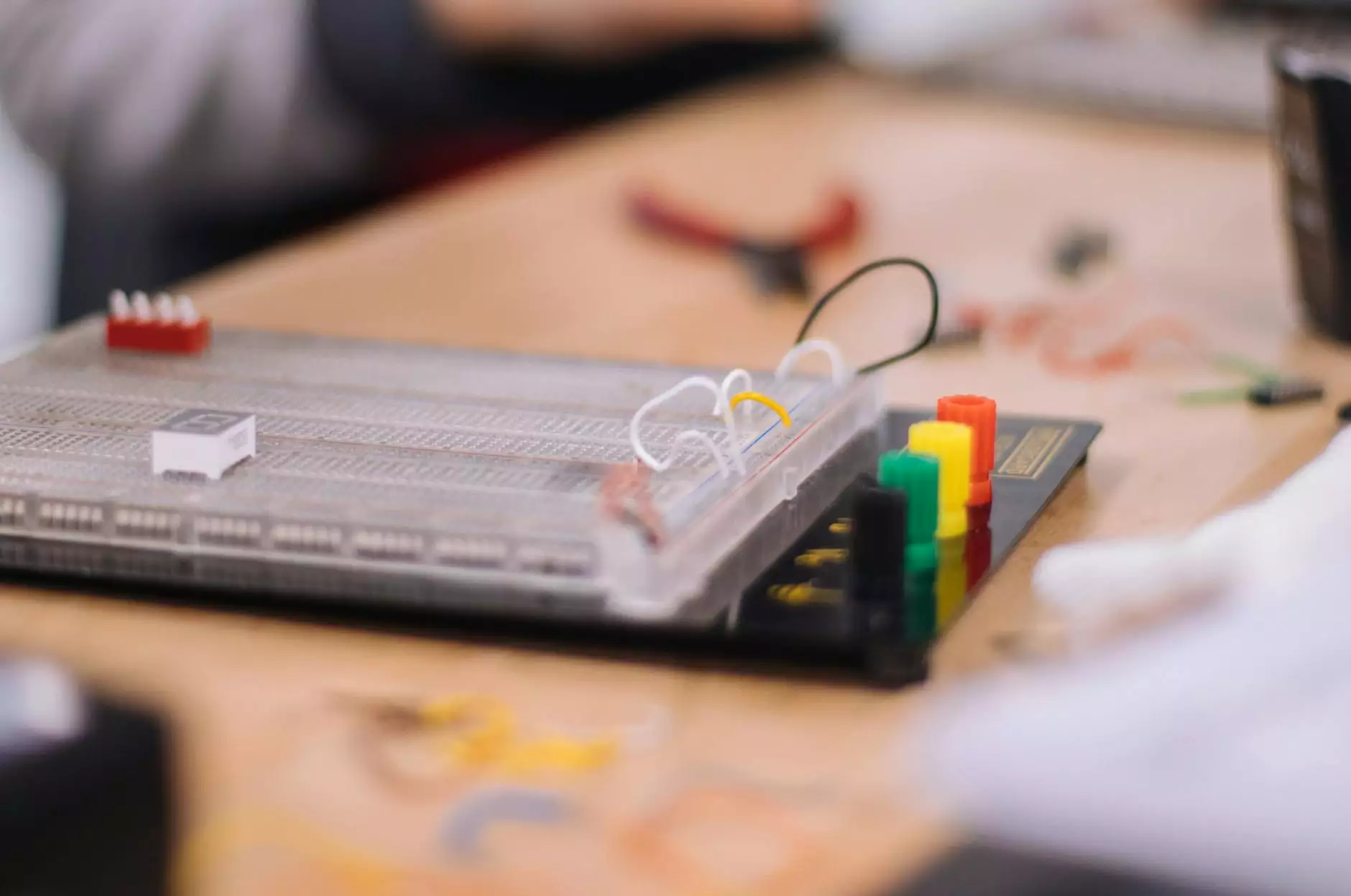
In today’s fiercely competitive and rapidly evolving marketplace, innovation is the lifeblood of sustained business success. Companies across industries are continually seeking methods to streamline their product development processes, reduce costs, and bring high-quality products to market faster. Among these revolutionary advancements, plastic rapid prototyping stands out as a game-changing technology that empowers businesses to transform their ideas into tangible, functional prototypes with unprecedented speed and precision.
Understanding Plastic Rapid Prototyping: A Key to Accelerated Innovation
Plastic rapid prototyping is a cutting-edge manufacturing process that leverages advanced 3D printing and additive manufacturing techniques to produce physical models of product components swiftly and accurately. Unlike traditional prototyping methods, which can take weeks or even months, plastic rapid prototyping offers a dramatic reduction in development time, enabling designers and engineers to evaluate their concepts almost instantly.
The Evolution and Importance of Rapid Prototyping in Business
Rapid prototyping emerged as a response to the need for faster, more efficient product development cycles. Initially restricted to simple models, modern plastic rapid prototyping incorporates sophisticated materials and techniques, allowing for intricate, detailed, and functional prototypes that closely resemble final production parts.
This evolution has revolutionized the way companies approach innovation. They can now identify potential flaws, assess ergonomics, and make design adjustments early in the development stage—saving significant time and money down the line. The importance of plastic rapid prototyping in today's business landscape cannot be overstated, especially for industries such as automotive, aerospace, consumer electronics, medical devices, and more.
Advantages of Plastic Rapid Prototyping for Business Growth
- Speed: Significantly reduces time-to-market by enabling rapid creation of prototype models, allowing faster iteration cycles.
- Cost-Effectiveness: Minimizes expenses associated with traditional mold-based prototype manufacturing, especially for low to medium volume production.
- Design Flexibility: Supports complex geometries, intricate details, and customized shapes that are difficult to achieve with traditional manufacturing methods.
- Enhanced Collaboration: Facilitates better communication among designers, engineers, and stakeholders by providing tangible models for review and testing.
- Risk Reduction: Allows early detection of design flaws and manufacturability issues, decreasing the likelihood of expensive revisions later in production.
- Customization Capability: Enables high levels of customization in prototypes, which is vital for personalized products and niche markets.
Comprehensive Materials Used in Plastic Rapid Prototyping
The success of plastic rapid prototyping largely depends on the selection of suitable materials. Various thermoplastics are used, each offering specific properties tailored to different prototype requirements. Common materials include:
- ABS (Acrylonitrile Butadiene Styrene): Known for durability, strength, and impact resistance, ideal for functional testing.
- PLA (Polylactic Acid): Environmentally friendly, easy to print, suitable for aesthetic models and display prototypes.
- polycarbonate: Exceptional toughness and temperature resistance, used for high-performance prototypes.
- PETG ( polyethylene terephthalate glycol): Offers good chemical resistance and clarity, suitable for transparent or semi-transparent prototypes.
- Flexibles (TPE, TPU): Used for prototypes requiring elastomeric properties, such as grips or flexible components.
Innovative Technologies Driving Plastic Rapid Prototyping
The landscape of plastic rapid prototyping is shaped by advanced manufacturing techniques, including:
- Stereolithography (SLA): Uses UV laser to cure liquid resin into solid parts with high resolution and surface finish.
- Fused Deposition Modeling (FDM): Melts thermoplastic filament to build prototypes layer by layer, widely accessible and cost-effective.
- Selective Laser Sintering (SLS): Uses a laser to sinter powdered materials, ideal for durable, functional prototypes with complex geometries.
- PolyJet Printing: Jetting layers of curable liquid photopolymer, offering high precision and smooth surface finishes close to injection-molded parts.
The Role of Plastic Rapid Prototyping in Different Industries
Automotive Industry
In automotive, plastic rapid prototyping accelerates the development of lightweight components, interior parts, and concept models. It allows designers to visualize and evaluate complex geometries early, reducing lead times and enhancing innovation.
Aerospace Sector
The aerospace industry benefits from high-strength, functional prototypes that meet strict safety standards. Plastic rapid prototyping supports testing aerodynamic models, cabin components, and ergonomic tools with precision and reliability.
Consumer Electronics
Rapid prototyping enables quick iteration of case designs, buttons, and internal structures, ensuring optimal user experience and aesthetic appeal before mass production.
Medical Devices
In healthcare, plastic rapid prototyping facilitates the creation of patient-specific implants, surgical tools, and testing devices, vastly improving customization and testing efficiency.
Why DeepMould.net is a Leading Choice for Plastic Rapid Prototyping and Metal Fabrication
DeepMould.net, recognized in the metal fabricators industry, offers unmatched expertise and cutting-edge technology in plastic rapid prototyping. Their integrated approach combines advanced 3D printing techniques with precision CNC machining, providing clients with high-quality, reliable prototypes tailored to their exact specifications.
By partnering with DeepMould.net, businesses gain access to:
- Expert consultation: Guidance on selecting suitable materials and manufacturing techniques for optimal results.
- State-of-the-art equipment: Utilization of the latest SLA, SLS, FDM, and PolyJet printers for diverse project needs.
- Fast turnaround times: Ensuring rapid delivery without compromising quality.
- High-quality finishing: Post-processing options including sanding, painting, and assembly for ready-to-test prototypes.
- Cost efficiency: Competitive pricing models, especially advantageous for small and medium-sized production runs.
Future Trends in Plastic Rapid Prototyping and Business Opportunities
The future of plastic rapid prototyping is promising, driven by breakthroughs in multi-material printing, nanotechnology, and AI-driven design optimization. These advancements will enable even faster, more accurate, and more functional prototypes that bridge the gap between concept and production seamlessly.
For businesses, embracing this technology creates numerous opportunities, including:
- Enhanced product innovation and differentiation
- Reduced development costs and time-to-market
- Improved customer engagement through customized prototypes
- Scalability in manufacturing with hybrid prototyping and production solutions
Final Thoughts: Embracing Plastic Rapid Prototyping to Propel Business Success
In conclusion, plastic rapid prototyping is no longer a futuristic concept but a crucial component of modern product development strategies. It enables companies to innovate rapidly, optimize designs, and cut costs—giving them a significant competitive advantage in their markets. As technology continues to evolve, the potential applications and benefits of plastic rapid prototyping will only expand, opening new avenues for business growth and technological advancement.
To stay ahead in a dynamic business environment, it is essential for companies to leverage the power of plastic rapid prototyping. Partnering with experienced providers like DeepMould.net ensures access to state-of-the-art solutions, expert guidance, and quality results that can transform ideas into market-ready products efficiently and effectively.