Understanding Plastic Moulded Parts: The Backbone of Modern Manufacturing
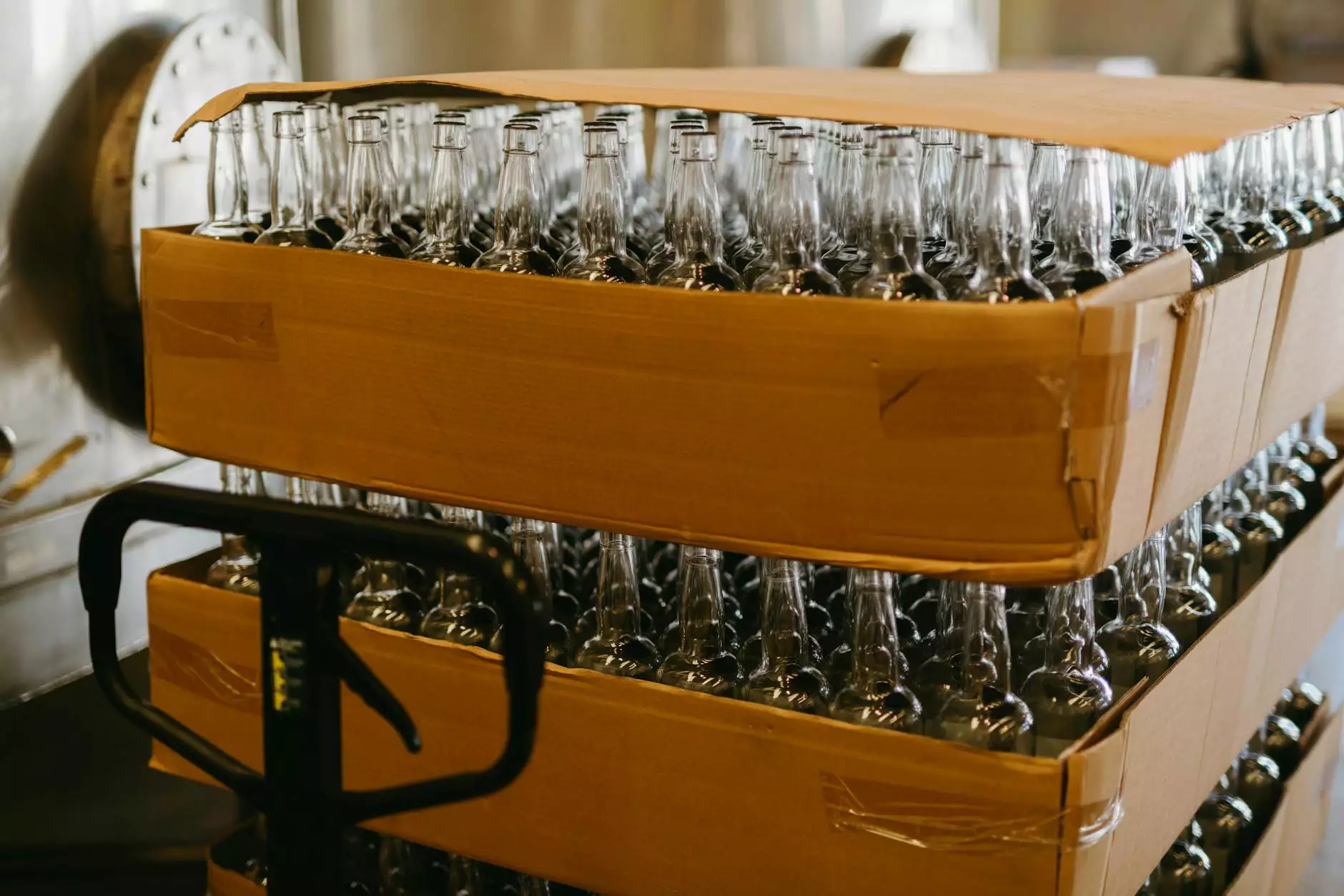
Plastic moulded parts play a vital role in the modern manufacturing landscape. From household items to intricate automotive components, the versatility and utility of these parts are indispensable. As industries continue to evolve, the demand for custom and efficient plastic moulding solutions is at an all-time high. This article delves into the world of plastic moulded parts, exploring their significance, applications, and the expertise offered by Hanking Mould, renowned for its excellence in plastic injection mould manufacturing.
The Essence of Plastic Moulded Parts
If we deconstruct the term, plastic moulded parts signify components manufactured using plastic materials that are shaped into specific designs through the process of moulding. This method allows for high levels of accuracy, repeatability, and efficiency, making it a staple in various industries.
Types of Plastic Moulding Processes
Understanding the different types of moulding processes is crucial for appreciating the diversity of plastic moulded parts. Here are the primary methods used in producing these components:
- Injection Moulding: This is the most prevalent method for creating plastic parts. In this process, molten plastic is injected into a mould cavity under high pressure.
- Blow Moulding: Primarily used for making hollow plastic products like bottles, this method involves inflating hot plastic inside a mould to create the desired shape.
- Thermoforming: This method involves heating a plastic sheet until it becomes pliable, then forming it into a specific shape using a mould.
- Rotational Moulding: Ideal for large hollow objects, rotational moulding involves rotating a heated mould filled with plastic to coat the interior surface.
The Advantages of Plastic Moulded Parts
Plastic moulded parts present numerous benefits that make them a preferred choice across various sectors:
- Cost-Effectiveness: The ability to mass-produce parts with minimal waste lowers the production costs significantly.
- Lightweight: Plastic is considerably lighter than metals and other materials, which reduces shipping costs and improves energy efficiency.
- Customizability: With advanced moulding techniques, manufacturers can create intricate designs tailored to specific requirements.
- Corrosion Resistance: Unlike metal parts, which can rust, plastic moulded components are resistant to corrosion, enhancing their lifespan.
- Ease of Manufacturing: The moulding process allows for rapid production cycles, making it ideal for businesses needing quick turnaround times.
Applications of Plastic Moulded Parts
The applications of plastic moulded parts are vast and varied, reflecting their importance in everyday life:
1. Automotive Industry
The automotive industry relies heavily on plastic moulded parts for manufacturing dashboards, panels, and various interior components. These parts contribute to weight reduction, which is crucial for fuel efficiency.
2. Consumer Goods
From toys to kitchen appliances, consumer goods are often enhanced through plastic moulded parts. Their ability to accommodate vibrant colors and diverse shapes makes them visually appealing and practical.
3. Electronics
Plastic components are essential in the electronics sector, where lightweight and insulative properties are needed. Items like mobile phone cases, circuit boards, and component housings are produced using sophisticated moulding techniques.
4. Medical Devices
The medical field utilizes plastic moulded parts for disposable items like syringes, IV bags, and various surgical instruments. The sterility and precision that moulding provides are critical in this sector.
5. Industrial Equipment
Various industrial applications rely on durable plastic components like gear wheels, housing enclosures, and piping systems, showcasing the versatility of plastic moulded parts in difficult environments.
The Role of Hanking Mould in Plastic Injection Moulding
At the forefront of the plastic moulding industry is Hanking Mould, a leading plastic mould maker and plastic injection mould manufacturer. With years of experience and a commitment to quality, Hanking Mould delivers exceptional moulding solutions that cater to various industries.
Why Choose Hanking Mould?
The following reasons make Hanking Mould a preferred choice for businesses seeking quality plastic moulded parts:
- Expertise: With a team of skilled professionals, Hanking Mould possesses extensive knowledge in designing and manufacturing high-quality moulds.
- Advanced Technology: Utilizing the latest technology in plastic injection moulding, Hanking Mould ensures precision and efficiency in production.
- Custom Solutions: Hanking Mould specializes in creating tailored solutions that meet the specific needs of clients, ensuring satisfaction with every product.
- Quality Assurance: With strict quality control protocols in place, Hanking Mould guarantees that all products meet industry standards.
- Commitment to Sustainability: Hanking Mould is dedicated to sustainable practices, focusing on minimizing waste and using environmentally friendly materials.
The Future of Plastic Moulded Parts
As technology advances, the future of plastic moulded parts looks promising. The integration of smart materials and sustainable practices is transforming the landscape of manufacturing. Innovations in bioplastics and recycling methods are paving the way for environmentally friendly solutions that will redefine the industry.
Trends Shaping the Industry
Several trends are emerging in the field of plastic moulded parts:
- Increased Automation: The rise of automation in manufacturing processes will enhance production efficiency and reduce costs.
- Sustainable Materials: The shift towards using recycled and biodegradable plastics is gaining momentum as companies strive for greener practices.
- 3D Printing Integration: The combination of 3D printing technology with traditional moulding processes is allowing for rapid prototyping and reduced lead times.
- Smart Manufacturing: The use of IoT and smart technologies in mould making and injection processes is enhancing monitoring and control.
Conclusion
In conclusion, plastic moulded parts are an integral aspect of modern manufacturing, underpinning a myriad of industries and applications. The expertise offered by Hanking Mould in the fields of plastic mould making and plastic injection mould manufacturing positions them as a trusted partner for businesses seeking quality and innovation. As the industry evolves, embracing technology and sustainability will be crucial in augmenting the capabilities and applications of plastic moulded parts in the future.
For more information on how Hanking Mould can assist with your plastic injection moulding needs, visit Hanking Mould today!